X1Jet MX
The Markoprint X1JET MX is an inkjet printer that runs independently. It’s ideal for coding large printing images directly on carton material in the food, beverage, chemical, and construction industries. On flat or absorbent surfaces, the MX Class piezo inkjet technology codes rapidly, correctly, and reliably.
The X1JET MX comes in three different styles: Compact, Vario, and Top. The print head on the Compact variant is fixed vertically. The Vario version’s print head may be rotated 90 degrees to the left for coding on ascending conveyor belts. The Top version codes to the packaging or product from above. True Type fonts are used to print text, logos, barcodes, and data matrix codes in the system.
The Markoprint X1JET MX makes printing simple with its 3-logic intuitive operation and LED status light. Data can be transferred via USB stick. It also has a maintenance station that includes a power supply.
Markoprint X1JET MX
Compact and well-prized piezo inkjet coder for large printing images
-
-
- Independent print system with Trident Piezo technology
-
-
-
- Cleaning station integrated with print system
-
-
-
- All-in-one – print head, ink system, cleaning station, control electronics and power supply
-
-
-
- Simple and intuitive 3-button operation with LED control lamps for user-friendly system controls
-
-
-
- Available as 50 or 100 mm print head
-
-
-
- As Compact, Top or Vario version
-
-
-
- With Scantrue ink
-
Adobe Reader is required to open and view PDF files. This can be downloaded free from adobe.com.
Available Documents
X1JET MX leafletInk Guide 2015
Markoprint Integra One ip LX
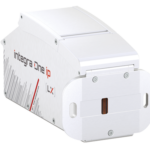
Unleash the Power of Proven Washdown Technology (IP Protection) for Seamless Performance in Complex and Demanding Applications. Experience High-Speed Printing and Effortless Operation with Up to 10 mm Print Distance. Discover Impressive Innovations, including a Patented Mechanism for Secure Ink/Printhead Unit Hold, Setting a New Standard in Printing Excellence.
View ProductZebra FS20 Fixed Industrial Scanner
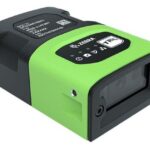
An Easily Integratable Scanning Solution
The increasing demands of international commerce and its global supply chain are pressuring companies to deliver more — and to do it faster. From manufacturing to logistics to the end customer, success is driven by the ability to quickly move and track the products that drive your business.
Address it all with the compact Zebra FS20 Fixed Industrial Scanner. With the FS20, it’s easy to track and trace every item as it moves through production, storage and fulfilment. Scan barcodes on components moving through your assembly line to ensure the right part is used at the right time — and enable rapid targeted recalls of products that contain defective parts. Scan barcodes on items as they are placed on warehouse shelves to provide visibility into real time inventory. And scan barcodes when fulfilling orders to ensure the right items are sent to the right customer. Whatever you want to track and trace, the FS20 makes it easy.
View ProductGeset 141 Semi Automatic Label Dispenser
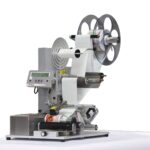
The Geset 141 semi-automatic all-round labelling system is used for labelling small tins, bottles, jars etc. This solution was developed especially for companies requiring flexible labelling of small batches. Classical applications include the pharmaceutical and cosmetics industry and the food and beverage sector.
View Product
Markoprint Integra Quadro/Quadro²
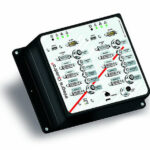
The new Markoprint Integra Quadro/Quadro² print controller can control up to four inkjet printers or four print positions at the same time. This allows you to print on both sides of primary and secondary packaging on one or two separate production lines. There are also two separate printing methods that can be used in this process.
The Markoprint Integra Quadro/Quadro² can easily cope with limited space thanks to its slender design. Installation inside or directly at the industrial line is straightforward thanks to the different fixation options. It was designed specifically for installation in control panels and machinery.
View Product