Trident
Trident is perfect for text, barcode and graphic marking on absorbent and smooth surfaces.It is easy to use, highly reliable and can reach printing speeds up to 60 meters per minute.
Click on the Direct Sales Button, and contact us today to order your Trident inkjet thermal inks.
- High reliability
Piezo-controlled graphic printing for industry-standard fonts, with almost unlimited number of rows.
- high printing speeds in barcode quality
up to 60 m/minute at 192 dpi (maximum 200 m/minute)
- good print image
based on perfected and proven Piezo technology
- simple operation
through integrated maintenance module
- unique flexibility
through the use of several Trident printheads
- Maximum 50 mm to 800 mm printing heights possible, as well as freely configurable layouts
- Multi-sided coding of packaging on two sides (top, side or at different production lines)
- virtually any porous surfaces can be marked, depending on ink type
- Topping up ink whilst in operation
- up to 5 mm distance from printhead to product surface enables marking of cartons with surface tolerances
- highly economical
- Best price-performance ratio in terms of ratio: cost of ink to area printed
Adobe Reader is required to open and view PDF files. This can be downloaded free from adobe.com.
Available Documents
Zebra FS10 Fixed Industrial Scanner
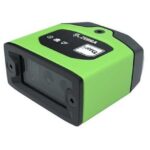
A Quick & Compact Scanning Solution
The increasing demands on international commerce and its global supply chain are pressurising businesses to deliver more and deliver faster. From manufacturing to logistics to the end customer, success is driven by the ability to move quickly and track the products that drive your business.
Now you can address it all with the compact Zebra FS10 Fixed Industrial Scanner. With a slim profile, the FS10 fits easily everywhere you need scanning. Just plug the FS10 into the USB port of a workstation, laptop, tablet or any other host device to dependably capture barcode data, from assembly to storage and fulfilment.
View ProductULTRAPRINT – High durability resin
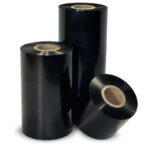
ULTRAPLATE is the standard resin ribbon from Weber. It is dedicated to
applications requiring a perfect printing quality and excellent mechanical
resistances. Its high versatility (it also prints on coated papers) and its
performances (sharpness, printing speed) have resulted in making
ULTRAPLATE a market reference.
Geset 141 Semi Automatic Label Dispenser
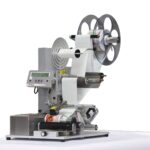
The Geset 141 semi-automatic all-round labelling system is used for labelling small tins, bottles, jars etc. This solution was developed especially for companies requiring flexible labelling of small batches. Classical applications include the pharmaceutical and cosmetics industry and the food and beverage sector.
View Product
Markoprint ZTV HP
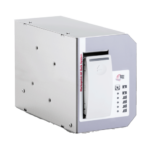
The Markoprint ZTV HP is a Central Ink Supply (CIS) system stores up to 400ml of ink for Markoprint HP Class inkjet printing systems such as the Markoprint integra One, Markoprint X2JET / X4JET, and Markoprint integra Quadro.
The large ink tank prevents frequent cartridge replacements from lowering your Overall Equipment Effectiveness (OEE). It can hold up to four single HP cartridges repaying you rapidly thanks to reduced ink prices. For non-interrupted production, the system can be paired with our NonStopPrinting printhead. Using an interface directly on the cartridge, current ink filling levels are monitored in real time. When the levels in the bulk tank fall below a certain threshold, a valve to the bulk tank opens and automatically refills it.
View Product