Tamper Evident
Compact label dispenser for protection against manipulation of pharmaceutical packaging.
The EU Directive 2011/62/EU promulgated in 2011 introduced legal framework requirements for a pan-European safety system for prevention of counterfeit medicines. A central component, which is also addressed in the pharmaceutical law, is a clear and secure marking system for database-backed traceability and tamper-proof sealing of all packaging. Bluhm System can offer a compact, efficient and reliable solution to this requirement. A compact labelling unit is integrated into existing data matrix stations or weighing systems. Self-adhesive label seals are applied on both sides of the flap openings of pharmaceutical packing. Perforation on the labels will expose manipulation by destruction of the labels. Depending on the packaging plant, labels are either dispensed after weighing or after an inkjet printer – e.g. the Markoprint series – has printed a sequential datamatrix code onto each package.
Following this, code and seal checking by a camera system is recommended. The package will be rejected if the marking is wrong or if a seal is applied incorrectly. Only OK products will leave the plant.
Special Features
- Sealing labelling for protection against counterfeits
- Two-sided corner labelling of folding boxes
- Highly compact design to allow integration into existing plant
- Output clocking up to 300 items per minute
- Stepper motor driven applicator
- Short set-up times when switching to other product formats
- Processing of transparent, perforated labels
- Speed-independent labelling via Tamp-Wipe-On method
- Dual label roll unwinding
Adobe Reader is required to open and view PDF files. This can be downloaded free from adobe.com.
Available Documents
Tamper Evident WeberDURAPRINT – Wax resin
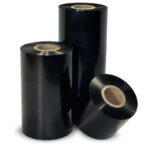
DURAPRINT is a very versatile, multi-purpose wax-resin ribbon.
It provides a higher level of resistances compared to standard wax ribbons and
prints small characters and barcodes with a high level of quality.
Zebra FS70 Fixed Industrial Scanner
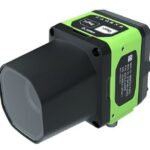
Today more than ever, the increasing demands of international commerce and its global supply chain are pressuring companies to deliver more — and to do it faster. From manufacturing to logistics to the end customer, success is driven by the ability to quickly move and track the products that drive your business.
The FS70 Fixed Industrial Scanner is your configurable and customisable solution. Easily keep pace with your business, enabling quality control and track-and-trace of every part and package as it moves through production, storage and fulfilment. Whether you need a high-powered lens to read a very small barcode from a long distance, or a wide-angle lens to capture barcodes on extremely large parts, the FS70 addresses it all. C-mount external lenses allow you to achieve the working range and field of view your application and environment requires. And compatibility with virtually any external lighting solution ensures reading of the most challenging barcodes — even low-contrast direct part marks or those printed on curved or reflective surfaces. The result? Best-in-class production, warehousing, distribution and logistics processes that inspire your business to reach its highest potential.
View Product
Markoprint Integra One
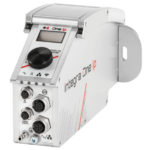
Labeling systems are not always easy to integrate into preexisting production lines. The Markoprint Integra One can be easily integrated into production processes thanks to its compact dimensions of 186 x 86 x 98 mm. The printing system has a display for data entry as well as system settings modification and verification. This information can also be viewed from mobile devices if the WLAN version is selected.
Inkjet printers should be properly protected if they are subjected to harsh manufacturing circumstances. In addition, the Markoprint integra One ip has an IP 65 protection rating. As a result, it’s ideal for use in the food industry.
View ProductZebra FS40 Fixed Industrial Scanner

Enable Performance. Inspire Potential. Experience The Difference.
Today more than ever, the increasing demands of international commerce and its global supply chain are pressuring companies to deliver more — and to do it faster. From manufacturing to logistics to the end customer, success is driven by the ability to quickly move and track the products that drive your business.
Address it all with Zebra’s FS40 Fixed Industrial Scanner designed to meet the comprehensive requirements of today’s production and delivery processes. The FS40 easily keeps pace with the fastest moving operations, enabling track-and-trace through the automatic and flawless decode of information on every part and package as it moves through production, storage and fulfilment — capturing even the most challenging barcodes. The result? Best-in-class production, warehousing, distribution and logistics processes that inspire businesses to reach their highest potential.
View Product