Weber LA 4050AC Shuttle
On Print and Apply Systems it is often the print module which determines the working rate. This is not the case with the new Legi-Air 4050 AC Shuttle. A loop device ensures a ready supply of labels which are custom-printed before being dispensed at unusually high speeds onto the passing products. The capacity of…
On Print and Apply Systems it is often the print module which determines the working rate. This is not the case with the new Legi-Air 4050 AC Shuttle.
A loop device ensures a ready supply of labels which are custom-printed before being dispensed at unusually high speeds onto the passing products. The capacity of this storage device means that even higher cycle speeds of short duration can be achieved. A check is kept on the loop by a dancer roller to ensure there is a supply of labels present. The benefits of this variant are
ease of use and the compact system design. Labelling capacity may be up to 20 times greater than printing capacity. Print speeds of up to 16 m per minute and conveyor speeds of up to 70 m per minute can be achieved.
Typical applications are labelling of identical products or products of continuous height. Compressed air is not required unlike most systems in the market today as the Print Apply System is completely electric and virtually Plug and Play. The result is a high level of cost-efficiency.
For partial printing on the label, print modules with automatic Ribbon Saver systems are available, resulting in further cost savings.
Technical specifications
Print technology
Thermal transfer or direct thermal
Dispensing method
Wipe-on
Print resolution
- 8 dots/mm (203 dpi)
- 12 dots/mm (300 dpi)
- 24 dots/mm (600 dpi)
Print speed
Up to 400 mm per second
Maximum throughput width
160 mm (option of 173 mm)
Label sizes
Maximum: 148 x 210 mm
Minimum: 14 x 10 mm
Maximum length of dispensing device
300 mm
Maximum take-off speed
70 m per minute, limited by label format
Minimum label gap
3 mm
Label roll
300 mm external diameter with up to 450 running metres, roll core of 76 mm(3“), outside winding, roll end advance warning Option: Inside winding, larger roll core diameter and 350 mm label roll external diameter
Data interfaces
All current interfaces (details in the print module brochure)
Control interfaces
Floating outputs (relays), optocoupler inputs, M12 connections for photocells and alarm lamps
Maintenance intervals
According to interval notice
Dispensing capacity
Up to 600 labels a minute; dispensing capacity depends on label size, text changeover and product speed
Positional accuracy of labels when dispensed
± 0.8 mm
Interchangeable dispensing device
Optional
Flexible print module technology
Datamax, Sato, Zebra, Avery PEM, CAB
Print dispenser activation
Reflex sensor, light barrier, inductive or capacitative sensor, microswitch, floating contacts (PLC)
Alarm device
Standard: Error messages in the text display, floating contacts (PLC)
Optional: Three-colour alarm lamp
Options
- RFID labelling
- Three-colour alarm LED
- Dust-protective housing (including with heating) for use in particularly problematic environments
- IPC inside the housing
- Legitronic® label print software
- Bluhmware for controlling and networking the systems
- Label presence monitor
- Scanner (1-D/2-D), vision systems, sensors, RFID gates
- Product detector
- Shaft encoder for variable product speed adjustment
- Frame in various versions (fixed, shaft-adjustable, mobile)
Adobe Reader is required to open and view PDF files. This can be downloaded free from adobe.com.
Available Documents
Legi-Air 4050 AC Shuttle leafletGeset 141 Semi Automatic Label Dispenser
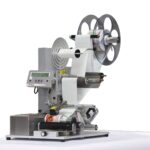
The Geset 141 semi-automatic all-round labelling system is used for labelling small tins, bottles, jars etc. This solution was developed especially for companies requiring flexible labelling of small batches. Classical applications include the pharmaceutical and cosmetics industry and the food and beverage sector.
View Product
Geset 112 Bottom Labelling System
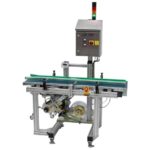
The Geset 112 labelling system is used to label square products on the bottom side automatically. Depending on the type and dimension of the product, different label sizes are used. The products are fed manually or by a conveying system provided by the customer at an infeed passage on the labelling system. Care should be taken on accurate alignment of the products. It is essential that the products are forwarded separately to the applicator with a gap between each other.
When the light barrier is reached, an application trigger is tripped. The label applicator applies then in Wipe On procedure a label onto the product. The label on bottom side is pushed on the product by the self-weight of the product. After labelling the products move on and can be removed from conveyor by the customer.
View ProductGeset 117 Top and Bottom Labelling System
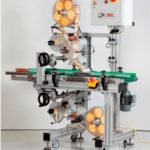
The Geset 117 labelling system is used to label square products on the top and bottom side automatically. Depending on the type and dimension of the product, different label sizes are used. The products are fed manually or by a conveying system provided by the customer at an infeed passage on the labelling system. Care should be taken on accurate alignment of the products. It is essential that the products are forwarded separately to the applicator with a gap between each other.
When the light barrier is reached, an application trigger is tripped. Both label applicators apply then in Wipe On procedure a label onto the product. The label on top side is pushed on the product by a brush or roller. The label on bottom side is pushed on the product by the self-weight of the product. After labelling the products move on and can be removed from conveyor by the customer.
View ProductGeset 111 Top Labelling System
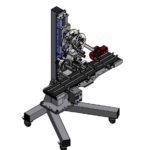
The Geset 111 labelling system is used to label square products on the top side automatically. Depending on the type and dimension of the product, different label sizes are used. The products are fed manually or by a conveying system provided by the customer at an infeed passage on the labelling system. Care should be taken on accurate alignment of the products. It is essential that the products are forwarded separately to the applicator with a gap between each other.
When the barrier is reached, an application trigger is tripped. The label applicator applies a label on the product in Wipe On procedure. The label on the top side is pushed on to the product by a brush or roller. After labelling, the products move on and can be removed from the conveyor by the customer.
View Product