Alpha Compact Inkjet
The Markoprint Weber Alpha Compact Inkjet system effectively applies labels with the addition of our X1-Jet TIJ coder for date and batch coding. A wide variety of fast drying inks and colors are available for a wide range of applications on diverse label surfaces.
Using cartridge ink technology, data of up to 12.5 mm high symbols and a resolution of up to 600 dpi can be printed neatly and quickly. Data transmission to the print head is 1:1 and real time printing without batch processing is also possible.
The Markoprint Weber Alpha Compact Inkjet system effectively applies labels with the addition of our X1-Jet TIJ coder for date and batch coding. A wide variety of fast drying inks and colors are available for a wide range of applications on diverse label surfaces.
- Printing of information such as text, shelf life, barcodes, 2D codes, graphics and logos
- Changing of print data via automatic functions or quick change of data by hand, directly at the applicator or via overriding
- Up to 3 000 serializations per minute and 600 dpi resolution, using cartridge printing technology
- Integrated and automatic date functions with expiry calculator and serial numbers
- Variable symbol heights from <1 to 12,5 mm
- Brilliant marking quality and maintenance-free functionality
- Immediate printing and high reliability, based on proven cartridge printing units
- A new printing unit with every ink cartridge replacement
- Printing in throughput mode in direction of travel, at various speeds
Adobe Reader is required to open and view PDF files. This can be downloaded free from adobe.com.
Available Documents
Alpha Compact X1JET leafletInk guide 2015
Geset 141 Semi Automatic Label Dispenser
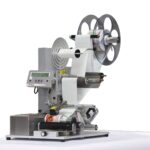
The Geset 141 semi-automatic all-round labelling system is used for labelling small tins, bottles, jars etc. This solution was developed especially for companies requiring flexible labelling of small batches. Classical applications include the pharmaceutical and cosmetics industry and the food and beverage sector.
View Product
Markoprint Integra PP RAZR
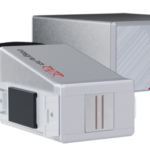
Experience Effortless High-Resolution Printing: Introducing the Integra PP RAZR with Cutting-Edge Technology. Print Up to 34mm High on Virtually Any Product Surface with Ease. Be Amazed by the Permanent Print Head’s Impressive Resolution, Lightning-Fast Speed, and Integrated Redundancy. Plus, its Compact Design Ensures Seamless Placement in Any Production Facility.
View ProductMarkoprint Integra PP 108
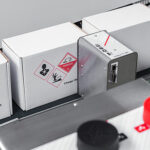
The Markoprint Integra PP108 is the first inkjet printer with SEIKO printing technology and a circulating ink system. It features a POZIFLOW circulating ink system which prevents the accumulation of air in the nozzles and ensures a permanent, clean print image without missing print due to blocked nozzles. The system’s ink tank can be installed above, below, or at the same height as the print head without any problems. The new SEIKO printhead has a print height of 108 mm and achieves a remarkable speed of up to 150 meters per minute with a high resolution of 360 dpi.
Suited to Dual Colour Printing Applications such as Hazard Labelling, Dual Colour overprinting and Direct Printing Applications to corrugate, and web printing applications, the PP108 is the latest high end, economical Inkjet System using the latest Drop on Demand Printing Technology.
View ProductGeset 112 Bottom Labelling System
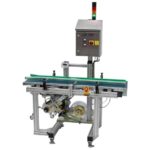
The Geset 112 labelling system is used to label square products on the bottom side automatically. Depending on the type and dimension of the product, different label sizes are used. The products are fed manually or by a conveying system provided by the customer at an infeed passage on the labelling system. Care should be taken on accurate alignment of the products. It is essential that the products are forwarded separately to the applicator with a gap between each other.
When the light barrier is reached, an application trigger is tripped. The label applicator applies then in Wipe On procedure a label onto the product. The label on bottom side is pushed on the product by the self-weight of the product. After labelling the products move on and can be removed from conveyor by the customer.
View Product