Industrial Label Printers – High Performance for High Demands
Weber Marking’s industrial label printers are the perfect solution for automatic printing and labelling. From small systems with a broad range of applications to high-end demands with specialised needs, every industrial label printer is durable and can operate to maximum efficiency.
All applications despite complexity can be accomplished accurately and swiftly. State-of-the-art technology will streamline your operations and implement every labelling task. Once set, our industrial label printers can print and position the labels automatically on every product, tray, package or pallet that is applied to your area of business.
Modular setting-up
Due to modular construction, Weber Marking’s industrial label printers can be set up for more than 1,500 different areas of operation. Depending on the label size of the rewinder or unwinder, Weber Marking can provide up to 600 linear metres per roll. Printing is available either as a direct thermal or a thermal transfer method. The standard resolution amounts to 203 dpi (8 dots per mm), but can be increased up to 600 dpi (24 dots per mm).
At maximum, printing speed can be completed at 400 mm per second according to the resolution. The standard tamp blow can handle labels of any size between 12,5 x 7 and 180 x 300 mm, but they are also exchangeable with purpose-built stamps for customised labels. The control section corresponds to specific needs and fully equipped with HOST connection, reflex button, light barrier, inductive or capacitive sensor and a SPS output microswitch. Finally, the data interface supports all standard formats and makes the industrial label printer an easy fit into already-established systems.
Weber’s industrial label printers size and scale can meet your requirements
These printers fulfill every aspect of high performance printing and are therefore offered in different sizes and scales:
- Entry class systems appeal to customers with minimum space requirements with very reasonable prices. They are easy to operate and suitable for many applications.
- Middle class systems come with a lightweight ab bnd compact design, which allows a fast replacement of the printing or stamp module. Their labelling process is also kept up to date with the ever-changing requirements and provides RFID-technology. Diagnostic routines, if necessary, can easily be monitored via text displays.
- High end systems deliver basic units suitable for standard and special applications. Thanks to their modular construction, these premium industrial label printers are robust devices fit for any demand. RFID can be applied to the full extent and includes, ‘flagtag’ for instance. Full graphic displays with touchscreens offer the full comfort for handling and maintenance.
Customised labelling system
Every customer and task is unique. Our industrial labelling systems can fulfill a range of printing tasks and dispense labels in a range of shapes for all kinds of materials. From paper and plastic to wood and steel. For the appropriate printing speed, the required resolution and the necessary label size – we can set-up a specially tailored system that fits perfectly your demands and needs using intelligent modular components. For the best in high performing industrial label printers, look to Weber.
Adobe Reader is required to open and view PDF files. This can be downloaded free from adobe.com.
Available Documents
print_and_applyGeset 111 Top Labelling System
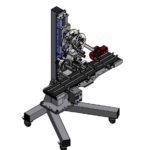
The Geset 111 labelling system is used to label square products on the top side automatically. Depending on the type and dimension of the product, different label sizes are used. The products are fed manually or by a conveying system provided by the customer at an infeed passage on the labelling system. Care should be taken on accurate alignment of the products. It is essential that the products are forwarded separately to the applicator with a gap between each other.
When the barrier is reached, an application trigger is tripped. The label applicator applies a label on the product in Wipe On procedure. The label on the top side is pushed on to the product by a brush or roller. After labelling, the products move on and can be removed from the conveyor by the customer.
View ProductGeset 141 Semi Automatic Label Dispenser
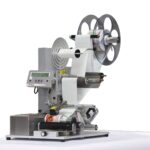
The Geset 141 semi-automatic all-round labelling system is used for labelling small tins, bottles, jars etc. This solution was developed especially for companies requiring flexible labelling of small batches. Classical applications include the pharmaceutical and cosmetics industry and the food and beverage sector.
View Product
Geset 117 Top and Bottom Labelling System
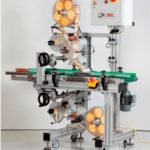
The Geset 117 labelling system is used to label square products on the top and bottom side automatically. Depending on the type and dimension of the product, different label sizes are used. The products are fed manually or by a conveying system provided by the customer at an infeed passage on the labelling system. Care should be taken on accurate alignment of the products. It is essential that the products are forwarded separately to the applicator with a gap between each other.
When the light barrier is reached, an application trigger is tripped. Both label applicators apply then in Wipe On procedure a label onto the product. The label on top side is pushed on the product by a brush or roller. The label on bottom side is pushed on the product by the self-weight of the product. After labelling the products move on and can be removed from conveyor by the customer.
View ProductGeset 112 Bottom Labelling System
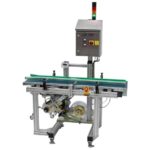
The Geset 112 labelling system is used to label square products on the bottom side automatically. Depending on the type and dimension of the product, different label sizes are used. The products are fed manually or by a conveying system provided by the customer at an infeed passage on the labelling system. Care should be taken on accurate alignment of the products. It is essential that the products are forwarded separately to the applicator with a gap between each other.
When the light barrier is reached, an application trigger is tripped. The label applicator applies then in Wipe On procedure a label onto the product. The label on bottom side is pushed on the product by the self-weight of the product. After labelling the products move on and can be removed from conveyor by the customer.
View Product