Legi-Air 5300
Label printer and dispenser for all labelling tasks
The new Legi-Air 5300 from Bluhm Systems is a modular Label printer and dispenser distinguished by its extremely versatile applications and a very high operating run time. In addition, the system offers a high degree of operator-friendliness: the operator is supported in his work by several functions such as service interval or operating condition display.
The Legi-Air 5300 is equipped with a variety of applicators for the most varied of tasks such as linear, rotation or corner applicators and also double-sided labelling. This guarantees the highest possible flexibility. Various label application methods are also possible including the tamp-blow and blow-box method for no-contact high speed labelling. For label printing there is a choice of industry-proven printing modules by many manufacturers. RFID printing modules for programming of radio chips are also available.
Legi-Air 5300: brilliant and high resolution
The system requires only one step to print the labels in brilliant and high resolution with a positional accuracy of up to ± 0.5 mm, or writes to RFID tags, with the information changing as required. Printing instructions can be stored directly in the system’s memory for easy handling, to be recalled again later by the operator. This enables working without a direct link to a PC.
Depending on applicator and application, label sizes of up to 180 x 500 mm can be processed and dispensing rates of up to 240 labels per minute are achievable. The system is suited for processing large label rolls with a maximum diameter of 350 mm (up to 600 m run length). In this way, it is not necessary to change the rolls as frequently and the operating run time is considerably increased.
Multilingual and user-friendly display
The multi-lingual plain language display is particularly user-friendly. It may be freely positioned in a way to best suit the operator even in constrained production environments such as under a conveyor system. Should there be a disruption such as the end of the working materials, the system can send an automatic report to an e-mail address previously specified by the operator.
The integrated service interval display will transmit a signal showing the next service date either to the conveyor system control or by e-mail. An integrated web browser can also be used to check the current service state. It is also possible to perform remote diagnosis via the browser.
The robust and enduring construction also renders the Legi-Air 5300 suitable for applications in rough production environments.
Adobe Reader is required to open and view PDF files. This can be downloaded free from adobe.com.
Available Documents
Legi-Air-5300-leafletGeset 125 Horizontal Labelling System
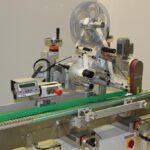
The Geset 125 labelling system is used to label cylindrical products automatically. Depending on the type and dimension of the product, different label sizes are used. The products are fed manually or by a conveying system provided by the customer at an infeed passage of the labelling system. Care should be taken on accurate alignment of the products between the two freely mounted rollers of the roll conveyor. The side guide’s position the products flush with the outside edge of the roll conveyor.
The roll conveyor feeds the products to the labeller. There the label is applied with the part running forward onto the product and it is pushed by rotation and the back pressure of the wrapping unit onto the product. The back pressure of the wrapping unit (the speed of the wrapping unit is twice as fast as the speed of the base conveyor) enables the product in rotation. The roll conveyor forwards the finished labelled products to the outfeed. Here the products are removed manually or by the customer’s conveying system.
View ProductGeset 111 Top Labelling System
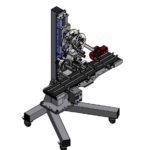
The Geset 111 labelling system is used to label square products on the top side automatically. Depending on the type and dimension of the product, different label sizes are used. The products are fed manually or by a conveying system provided by the customer at an infeed passage on the labelling system. Care should be taken on accurate alignment of the products. It is essential that the products are forwarded separately to the applicator with a gap between each other.
When the barrier is reached, an application trigger is tripped. The label applicator applies a label on the product in Wipe On procedure. The label on the top side is pushed on to the product by a brush or roller. After labelling, the products move on and can be removed from the conveyor by the customer.
View ProductGeset 117 Top and Bottom Labelling System
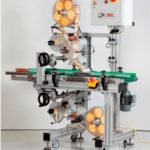
The Geset 117 labelling system is used to label square products on the top and bottom side automatically. Depending on the type and dimension of the product, different label sizes are used. The products are fed manually or by a conveying system provided by the customer at an infeed passage on the labelling system. Care should be taken on accurate alignment of the products. It is essential that the products are forwarded separately to the applicator with a gap between each other.
When the light barrier is reached, an application trigger is tripped. Both label applicators apply then in Wipe On procedure a label onto the product. The label on top side is pushed on the product by a brush or roller. The label on bottom side is pushed on the product by the self-weight of the product. After labelling the products move on and can be removed from conveyor by the customer.
View ProductGeset 112 Bottom Labelling System
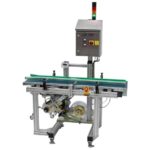
The Geset 112 labelling system is used to label square products on the bottom side automatically. Depending on the type and dimension of the product, different label sizes are used. The products are fed manually or by a conveying system provided by the customer at an infeed passage on the labelling system. Care should be taken on accurate alignment of the products. It is essential that the products are forwarded separately to the applicator with a gap between each other.
When the light barrier is reached, an application trigger is tripped. The label applicator applies then in Wipe On procedure a label onto the product. The label on bottom side is pushed on the product by the self-weight of the product. After labelling the products move on and can be removed from conveyor by the customer.
View Product