Model 4300 Pro-Apply Tamp-Blow Label Printer-Applicator
Weber’s economical Model 4300 Pro-Apply printer-applicators feature the functionality often limited to higher-duty production systems.
• Applies labels up to 6″ wide x 6″ long
• Prints text, bar codes and graphic images @ 203, 300 or 600 dpi
• Non-contact, tamp-blow application
• Accurate labelling to within ±0.03″
Model 4300 Pro-Apply Tamp-Blow Label Printer-Applicator
The Model 4300 Pro-Apply is a versatile in-line system that combines high quality label printing and application that ensures fast, accurate pressure-sensitive labelling.
The Model 4300 Pro-Apply system is designed and engineered by Weber and is assembled in our own U.S. manufacturing facility. Each unit is equipped with an on-demand, thermal/thermal-transfer print engine from Datamax, SATO or Zebra to produce 203, 300 or 600 dpi text, bar codes and graphic images at speeds up to 16 ips.
Labels up to 6″ wide and 6″ long are printed in a cost-efficient, next-out mode and are then instantly applied to cartons or products on the production or packaging line.
Utilising the tamp-blow method of application, a printed pressure-sensitive label is automatically peeled from its liner and is retained by vacuum on the applicator’s tamp pad. The pad is extended (select from 2″ to 12″ strokes) and blown onto the package from approximately 0.25″.
Several standard tamp-pad sizes are available and are provided in quick-change configurations. In just a few seconds the tamp-pad can be removed and another fastened in its place to handle a different size label.
Standard features include durable anodized aluminium construction, an integrated user interface with LCD display, and numerous inputs/outputs to facilitate the use of a product sensor or other optional accessories and stepper motor-driven rewind.
Adobe Reader is required to open and view PDF files. This can be downloaded free from adobe.com.
Available Documents
4300Zebra FS10 Fixed Industrial Scanner
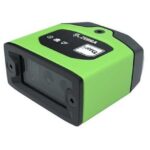
A Quick & Compact Scanning Solution
The increasing demands on international commerce and its global supply chain are pressurising businesses to deliver more and deliver faster. From manufacturing to logistics to the end customer, success is driven by the ability to move quickly and track the products that drive your business.
Now you can address it all with the compact Zebra FS10 Fixed Industrial Scanner. With a slim profile, the FS10 fits easily everywhere you need scanning. Just plug the FS10 into the USB port of a workstation, laptop, tablet or any other host device to dependably capture barcode data, from assembly to storage and fulfilment.
View ProductGeset 111 Top Labelling System
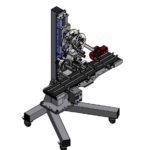
The Geset 111 labelling system is used to label square products on the top side automatically. Depending on the type and dimension of the product, different label sizes are used. The products are fed manually or by a conveying system provided by the customer at an infeed passage on the labelling system. Care should be taken on accurate alignment of the products. It is essential that the products are forwarded separately to the applicator with a gap between each other.
When the barrier is reached, an application trigger is tripped. The label applicator applies a label on the product in Wipe On procedure. The label on the top side is pushed on to the product by a brush or roller. After labelling, the products move on and can be removed from the conveyor by the customer.
View ProductEASYMARK – Standard Wax
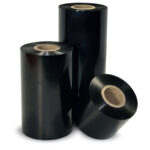
EASYMARK is the standard Weber wax ribbon which delivers consistent print
quality on any kind of paper label materials. It prints high density legible
barcodes and traceability data for short life labeling needs.
Markoprint Integra PP RAZR
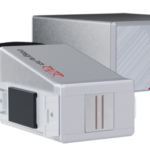
Experience Effortless High-Resolution Printing: Introducing the Integra PP RAZR with Cutting-Edge Technology. Print Up to 34mm High on Virtually Any Product Surface with Ease. Be Amazed by the Permanent Print Head’s Impressive Resolution, Lightning-Fast Speed, and Integrated Redundancy. Plus, its Compact Design Ensures Seamless Placement in Any Production Facility.
View Product