SB1-HC Smart Badge
Improving Quality of Care and Patient Experience
In order to maintain efficient workflows that protect patient safety, healthcare staff need to scan and track medications and medical tasks to ensure every task is completed on time, every time. The SB1-HC, the first device of its kind, offers a compact, wearable, powerful, and convenient means to meet all these demands, for every healthcare staff member. Now, the entire staff is connected, and they are never more than the press of a button away when an urgent answer to a question is required.
SB1-HC Key Features and Benefits
Small, lightweight and wearable
The compact, light SB1-HC is easily worn on a lanyard, belt clip, or armband, where it is available on demand to healthcare staff in an instant.
Built for constant disinfecting
Special plastics and IP54 sealing enable regular disinfecting wipe downs required to prevent the spread of germs between patients and caregivers.
Enterprise-class push-to-talk
At the press of a button, an SB1-HC user can talk to other staff who are carrying virtually any mobile device — an SB1-HC, a Zebra mobile computer (such as the MC40), a two-way radio or popular third party smartphones.1
Full shift power
The SB1-HC provides the peace of mind that comes with knowing workers will always have more than ample power for a full shift. The low-power E Ink® display provides over 14 hours of battery life from a single charge. And in badge mode, the screen can display a healthcare worker’s picture and name whenever the device is not in use — yet draw virtually no power at all.
Easy ‘touch’ navigation
Finger-style navigation eliminates the need for a stylus and supports a gloved hand.
Easily connect to wireless networks
With Zebra’s Wi-Fi 802.11b/g/n radio, healthcare staff members get a secure and solid wireless connection to any WLAN — so voice and data features are simply always available.
Adobe Reader is required to open and view PDF files. This can be downloaded free from adobe.com.
Available Documents
sb1-hc Spec SheetMarkoprint IP-Jet
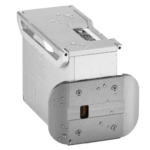
The thermal inkjet printer IP-JET HP MK3 has been specifically designed for usage in dusty or damp situations. It is especially ideal for the food sector, as well as the plastics, pharmaceutical, and chemical industries, due to its IP65 protection level.
The IP-JET HP is a small inkjet printer with a printhead and control unit housed in one unit. Water and dust are kept out of the cartridge by sealing it and pressurizing it. The power supply features a waterproof connector, and the external connections’ connectors are secured with an IP67 rating. The printhead does not need to be covered or removed for wet cleaning, unlike many other printers on the market.
View ProductGeset 111 Top Labelling System
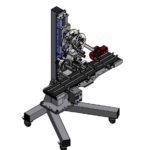
The Geset 111 labelling system is used to label square products on the top side automatically. Depending on the type and dimension of the product, different label sizes are used. The products are fed manually or by a conveying system provided by the customer at an infeed passage on the labelling system. Care should be taken on accurate alignment of the products. It is essential that the products are forwarded separately to the applicator with a gap between each other.
When the barrier is reached, an application trigger is tripped. The label applicator applies a label on the product in Wipe On procedure. The label on the top side is pushed on to the product by a brush or roller. After labelling, the products move on and can be removed from the conveyor by the customer.
View ProductZebra FS20 Fixed Industrial Scanner
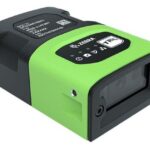
An Easily Integratable Scanning Solution
The increasing demands of international commerce and its global supply chain are pressuring companies to deliver more — and to do it faster. From manufacturing to logistics to the end customer, success is driven by the ability to quickly move and track the products that drive your business.
Address it all with the compact Zebra FS20 Fixed Industrial Scanner. With the FS20, it’s easy to track and trace every item as it moves through production, storage and fulfilment. Scan barcodes on components moving through your assembly line to ensure the right part is used at the right time — and enable rapid targeted recalls of products that contain defective parts. Scan barcodes on items as they are placed on warehouse shelves to provide visibility into real time inventory. And scan barcodes when fulfilling orders to ensure the right items are sent to the right customer. Whatever you want to track and trace, the FS20 makes it easy.
View ProductMarkoprint Integra One
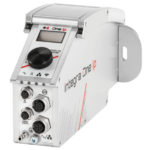
Labeling systems are not always easy to integrate into preexisting production lines. The Markoprint Integra One can be easily integrated into production processes thanks to its compact dimensions of 186 x 86 x 98 mm. The printing system has a display for data entry as well as system settings modification and verification. This information can also be viewed from mobile devices if the WLAN version is selected.
Inkjet printers should be properly protected if they are subjected to harsh manufacturing circumstances. In addition, the Markoprint integra One ip has an IP 65 protection rating. As a result, it’s ideal for use in the food industry.
View Product