Deli Labels
We can work with you to create amazing looking labels that will work with your container and handle the environmental conditions that it will be stored in like refrigeration or moisture. Your label has to not only keep your product safe but also needs to entice the customer into buying your product. Bright colors, metallic foils, clear films and more are just some of the design options that will set you apart from the crowd.
A Deli department usually has hundreds of different shaped containers and packages for all the delicious foods they sell. All those odd-shaped containers need labels. And the labels have to look good.
Deli Label Tips
Materials:
- Use a clear label material or metallic foils for the look of quality and to create dimensional effects with your label.
- Be sure to use label materials that will stand up to damp and/or refrigerated conditions.
- Always test your label adhesives to make sure they will stick securely to your containers, especially plastic clamshells and other non-paper materials.
Artwork:
- Use unique designs and colors to create a family of products. This makes it easier for consumer to return to your brand by sight.
- Keep your design simple but eye-catching. Create patterns on your label or subtle designs using dull or gloss varnishes.
- Custom die shapes allow you to use interesting shapes for your label.
- Add a QR code so your customers can interact with your company, get coupons, recipes and more.
Adobe Reader is required to open and view PDF files. This can be downloaded free from adobe.com.
Available Documents
X1Jet HP Premium MK2
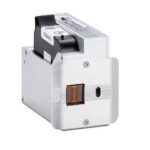
The innovative Markoprint X1JET HP inkjet printer codes absorbent and semi-absorbent surfaces quickly, accurately and reliably. It is designed for a different range of applications in the food and beverage industry as well as the chemical and pharmaceutical industry. The controller and printer are combined in one single unit, making the system extremely compact.
View ProductZebra FS20 Fixed Industrial Scanner
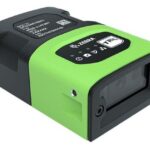
An Easily Integratable Scanning Solution
The increasing demands of international commerce and its global supply chain are pressuring companies to deliver more — and to do it faster. From manufacturing to logistics to the end customer, success is driven by the ability to quickly move and track the products that drive your business.
Address it all with the compact Zebra FS20 Fixed Industrial Scanner. With the FS20, it’s easy to track and trace every item as it moves through production, storage and fulfilment. Scan barcodes on components moving through your assembly line to ensure the right part is used at the right time — and enable rapid targeted recalls of products that contain defective parts. Scan barcodes on items as they are placed on warehouse shelves to provide visibility into real time inventory. And scan barcodes when fulfilling orders to ensure the right items are sent to the right customer. Whatever you want to track and trace, the FS20 makes it easy.
View ProductMarkoprint Integra Ultimate
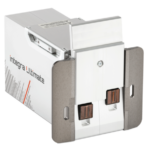
The innovative Integra Ultimate thermal inkjet printer not only provides IP65 protection against dust and moisture, but it also closes and cleans the nozzle plate at each pause. This system ensures that the printing is always clean, with faultless results even after extended breaks. As a result, the ink cartridges’ open times are multiplied many times. Two HP Class thermal inkjet ink cartridges can be used with the print head. As a result, the system produces beautiful prints with a maximum height of 25 mm.
View ProductGeset 112 Bottom Labelling System
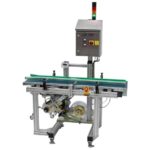
The Geset 112 labelling system is used to label square products on the bottom side automatically. Depending on the type and dimension of the product, different label sizes are used. The products are fed manually or by a conveying system provided by the customer at an infeed passage on the labelling system. Care should be taken on accurate alignment of the products. It is essential that the products are forwarded separately to the applicator with a gap between each other.
When the light barrier is reached, an application trigger is tripped. The label applicator applies then in Wipe On procedure a label onto the product. The label on bottom side is pushed on the product by the self-weight of the product. After labelling the products move on and can be removed from conveyor by the customer.
View Product