Model 5300 Series Air-Blow Label Printer-Applicator
This Weber exclusive provides high-resolution printing and high-speed operation combined with the dependable air-blow method of label application.
•Choose from a wide range of 203, 300 and 600 dpi print engines
•Capable of handling print speeds up to 16 ips
•Numerous I/O’s ease interfacing with external devices
•Monitor operation via a web browser
•Available with RFID capability
Model 5300 Series Air-Blow Label Printer-Applicator
Weber’s Model 5300 air-blow module provides an accurate, versatile means of pressure-sensitive label printing and non-contact application.
In addition to offering a broad selection of high-quality print engines that feature various print resolutions and label dispensing rates, this Model 5300 system is available with optional RFID print-encode engines.
Standard direct and thermal-transfer print engines from manufacturers Zebra, SATO and Datamax produce text, bar codes and graphic images at 203, 300 or 600 dpi. The Zebra-based RFID models combine these printing capabilities with the encoding and verification of RFID inlays to meet EPC Gen 2 protocols.
Special Features & Options
The Model 5300 air-blow system includes a number of noteworthy features that add to the operational versatility of this printer-applicator.
• Air-blow application: This method of air-assisted, fixed-distance label placement can be used with standard applications. A printed label is fed into place and held by vacuum, then it is blown onto a product or package to a placement accuracy of ±0.03″.
• Browser-based monitoring: The status of all operational functions and configurations can be monitored by logging on to a web page that is unique to each Model 5300 unit.
• Numerous I/O’s: The system can be interfaced with many types of external devices.
• One-to-one media consumption: Special label unwind and rewind dimensions are matched to the system’s ribbon supply to ensure they are consumed at the same rate, reducing downtime and eliminating partial changeovers.
• Print job storage: Multiple label printing formats can be stored in the system’s memory, making it easier for an operator to select a job directly from the applicator instead of downloading a computer file.
The Model 5300 air-blow system boasts numerous additional features including an upgradeable microprocessor controller, various inputs/outputs, plus durable construction that will withstand harsh industrial environments.
There are also several optional enhancements that can increase the system’s functionality. A product height sensor, for example, enables the printer-applicator to label items of varying heights delivered by the same conveyor.
Other options include a 15-foot umbilical connection that enables the remote location of the unit’s controller; an adjustable stand for optimum system orientation; label-on-pad and product-presence sensors; plus beacon light alerts to signal the status of label and ribbon supplies.
Adobe Reader is required to open and view PDF files. This can be downloaded free from adobe.com.
Available Documents
5300Geset 117 Top and Bottom Labelling System
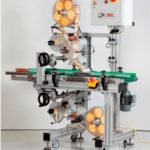
The Geset 117 labelling system is used to label square products on the top and bottom side automatically. Depending on the type and dimension of the product, different label sizes are used. The products are fed manually or by a conveying system provided by the customer at an infeed passage on the labelling system. Care should be taken on accurate alignment of the products. It is essential that the products are forwarded separately to the applicator with a gap between each other.
When the light barrier is reached, an application trigger is tripped. Both label applicators apply then in Wipe On procedure a label onto the product. The label on top side is pushed on the product by a brush or roller. The label on bottom side is pushed on the product by the self-weight of the product. After labelling the products move on and can be removed from conveyor by the customer.
View ProductGeset 125 Horizontal Labelling System
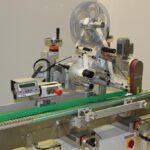
The Geset 125 labelling system is used to label cylindrical products automatically. Depending on the type and dimension of the product, different label sizes are used. The products are fed manually or by a conveying system provided by the customer at an infeed passage of the labelling system. Care should be taken on accurate alignment of the products between the two freely mounted rollers of the roll conveyor. The side guide’s position the products flush with the outside edge of the roll conveyor.
The roll conveyor feeds the products to the labeller. There the label is applied with the part running forward onto the product and it is pushed by rotation and the back pressure of the wrapping unit onto the product. The back pressure of the wrapping unit (the speed of the wrapping unit is twice as fast as the speed of the base conveyor) enables the product in rotation. The roll conveyor forwards the finished labelled products to the outfeed. Here the products are removed manually or by the customer’s conveying system.
View ProductZebra FS70 Fixed Industrial Scanner
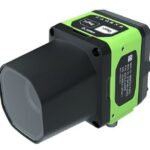
Today more than ever, the increasing demands of international commerce and its global supply chain are pressuring companies to deliver more — and to do it faster. From manufacturing to logistics to the end customer, success is driven by the ability to quickly move and track the products that drive your business.
The FS70 Fixed Industrial Scanner is your configurable and customisable solution. Easily keep pace with your business, enabling quality control and track-and-trace of every part and package as it moves through production, storage and fulfilment. Whether you need a high-powered lens to read a very small barcode from a long distance, or a wide-angle lens to capture barcodes on extremely large parts, the FS70 addresses it all. C-mount external lenses allow you to achieve the working range and field of view your application and environment requires. And compatibility with virtually any external lighting solution ensures reading of the most challenging barcodes — even low-contrast direct part marks or those printed on curved or reflective surfaces. The result? Best-in-class production, warehousing, distribution and logistics processes that inspire your business to reach its highest potential.
View Product
Markoprint Integra Quadro/Quadro²
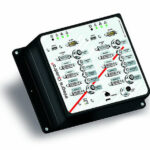
The new Markoprint Integra Quadro/Quadro² print controller can control up to four inkjet printers or four print positions at the same time. This allows you to print on both sides of primary and secondary packaging on one or two separate production lines. There are also two separate printing methods that can be used in this process.
The Markoprint Integra Quadro/Quadro² can easily cope with limited space thanks to its slender design. Installation inside or directly at the industrial line is straightforward thanks to the different fixation options. It was designed specifically for installation in control panels and machinery.
View Product