U-60 Label Dispenser
The Dispensa-Matic U-60 is ideal for dispensing pressure-sensitive labels from 0.375″ up to 6.0″ wide. Labels are peeled from their liner and presented to the user for easy grab and go labelling.
This semi-automatic electric label dispensing system is built to last using high-quality metal parts for years of service with little downtime. The U-60 is made in the USA and comes with a 3-year warranty.
U-60 Label Dispenser
The Dispensa-Matic U-60 Label Dispenser is a heavy-duty, semi-automatic electric label dispenser for labels from 0.375″ to 6.0″ wide x 0.375″ to any length. This label dispenser advances at over 7″ per second.
Features include:
Butt-cut or die-cut label compatible
Multiple row compatible
- Semi-automatic dispenser: pick, apply and repeat
- Label cartons, envelopes, brochures, bottles, bags, cans – anything that needs a label
- Side frames are made from the highest quality metals, then formed, countersunk, de burred and inspected
- Dispensing tables are formed out of aircraft-grade aluminium. The peel edge is hand-milled to spec within .001″
- Dispensing tables are polished with ultra-fine polishing compound so paper flows freely around the plate
- The U-60 motor is a shaded-pole AC motor
- Dispensa-Matic U-60 uses Micro-Switch branded switches, which are specifically designed to detect all kinds of labels: paper, Mylar, foil, holographic and clear; photo cell available
- International compatibility; motor is compatible for Europe and all other 220V 50/60hz
- Dimensions: 11″ x 13″ x 8″
- Weight: 13 lbs
Adobe Reader is required to open and view PDF files. This can be downloaded free from adobe.com.
Available Documents
X1Jet HP Premium MK2
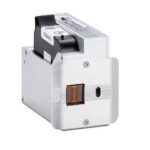
The innovative Markoprint X1JET HP inkjet printer codes absorbent and semi-absorbent surfaces quickly, accurately and reliably. It is designed for a different range of applications in the food and beverage industry as well as the chemical and pharmaceutical industry. The controller and printer are combined in one single unit, making the system extremely compact.
View ProductMarkoprint Integra Ultimate
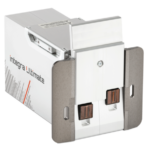
The innovative Integra Ultimate thermal inkjet printer not only provides IP65 protection against dust and moisture, but it also closes and cleans the nozzle plate at each pause. This system ensures that the printing is always clean, with faultless results even after extended breaks. As a result, the ink cartridges’ open times are multiplied many times. Two HP Class thermal inkjet ink cartridges can be used with the print head. As a result, the system produces beautiful prints with a maximum height of 25 mm.
View ProductZebra FS20 Fixed Industrial Scanner
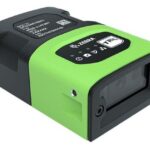
An Easily Integratable Scanning Solution
The increasing demands of international commerce and its global supply chain are pressuring companies to deliver more — and to do it faster. From manufacturing to logistics to the end customer, success is driven by the ability to quickly move and track the products that drive your business.
Address it all with the compact Zebra FS20 Fixed Industrial Scanner. With the FS20, it’s easy to track and trace every item as it moves through production, storage and fulfilment. Scan barcodes on components moving through your assembly line to ensure the right part is used at the right time — and enable rapid targeted recalls of products that contain defective parts. Scan barcodes on items as they are placed on warehouse shelves to provide visibility into real time inventory. And scan barcodes when fulfilling orders to ensure the right items are sent to the right customer. Whatever you want to track and trace, the FS20 makes it easy.
View ProductGeset 111 Top Labelling System
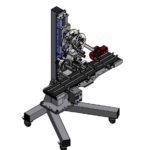
The Geset 111 labelling system is used to label square products on the top side automatically. Depending on the type and dimension of the product, different label sizes are used. The products are fed manually or by a conveying system provided by the customer at an infeed passage on the labelling system. Care should be taken on accurate alignment of the products. It is essential that the products are forwarded separately to the applicator with a gap between each other.
When the barrier is reached, an application trigger is tripped. The label applicator applies a label on the product in Wipe On procedure. The label on the top side is pushed on to the product by a brush or roller. After labelling, the products move on and can be removed from the conveyor by the customer.
View Product