Weber 114 One-Sided/Two-Sided Labelling System
The brand-new Weber 114 system provides a simple, cost-effective solution to low volume labelling for applying labels to one or two sides of a straight-walled product or package. The Model 114 can be added to in-place production lines or operated manually as a stand-alone applicator.
The Weber 114 is easy to use and can be set-up quickly. During application, labels are peeled away from the liner and securely attached to products using the wipe-on label applicators.
The unit boasts robust steel construction making it perfect for lower-volume, intermittent labelling projects or multiple-shift larger-scale operations. This is a very reliable wipe-on application system that is built to last.
-
-
- Applies label up to 6″ high x 12″ long
-
-
-
- Handles up to 45 products/minute
-
-
-
- Placement accuracy of 0.03″
-
Each version of the Alpha Compact features rugged die-cast aluminium construction, single-key calibration, automatic recognition of missing labels, in-production speed adjustment and more.
The controller for the Weber 114 features a display HMI that replaces the operator’s panel with an LCD display that provides full access to all adjustment parameters.
Adobe Reader is required to open and view PDF files. This can be downloaded free from adobe.com.
Available Documents
Geset 114 Technical InformationGeset 114 Computer Assisted Design
Markoprint Integra PP 108
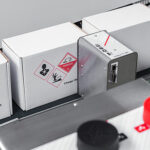
The Markoprint Integra PP108 is the first inkjet printer with SEIKO printing technology and a circulating ink system. It features a POZIFLOW circulating ink system which prevents the accumulation of air in the nozzles and ensures a permanent, clean print image without missing print due to blocked nozzles. The system’s ink tank can be installed above, below, or at the same height as the print head without any problems. The new SEIKO printhead has a print height of 108 mm and achieves a remarkable speed of up to 150 meters per minute with a high resolution of 360 dpi.
Suited to Dual Colour Printing Applications such as Hazard Labelling, Dual Colour overprinting and Direct Printing Applications to corrugate, and web printing applications, the PP108 is the latest high end, economical Inkjet System using the latest Drop on Demand Printing Technology.
View ProductZebra ZT510 Industrial Printer
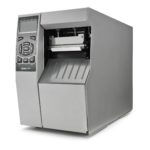
ZEBRA ZT510 – NEXT-GENERATION PRINTING THAT IS BUDGET-FRIENDLY
Designed to strike the ideal balance between performance and value, the Zebra ZT510 includes the core features you need in an industrial printer at a cost-effective price point.
View ProductMarkoprint Integra Quadro/Quadro²
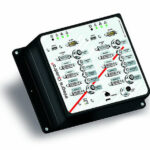
The new Markoprint Integra Quadro/Quadro² print controller can control up to four inkjet printers or four print positions at the same time. This allows you to print on both sides of primary and secondary packaging on one or two separate production lines. There are also two separate printing methods that can be used in this process.
The Markoprint Integra Quadro/Quadro² can easily cope with limited space thanks to its slender design. Installation inside or directly at the industrial line is straightforward thanks to the different fixation options. It was designed specifically for installation in control panels and machinery.
View ProductMarkoprint IP-Jet
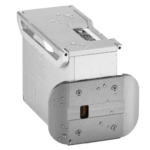
The thermal inkjet printer IP-JET HP MK3 has been specifically designed for usage in dusty or damp situations. It is especially ideal for the food sector, as well as the plastics, pharmaceutical, and chemical industries, due to its IP65 protection level.
The IP-JET HP is a small inkjet printer with a printhead and control unit housed in one unit. Water and dust are kept out of the cartridge by sealing it and pressurizing it. The power supply features a waterproof connector, and the external connections’ connectors are secured with an IP67 rating. The printhead does not need to be covered or removed for wet cleaning, unlike many other printers on the market.
View Product