Weber LA 4050S
Thanks to its robust and compact design, the Legi-Air 4050 S is always ready for the most diverse of labeling tasks. The modular design of the Legi-Air 4050 S offers companies the flexibility of responding to changing labeling demands at any time. Legi-Air 4050 S system advantages at a glance Versatile application for labeling…
Thanks to its robust and compact design, the Legi-Air 4050 S is always ready for the most diverse of labeling tasks. The modular design of the Legi-Air 4050 S offers companies the flexibility of responding to changing labeling demands at any time.
Legi-Air 4050 S system advantages at a glance
- Versatile application for labeling of cartons, sacking and pallets on one side
- Labeling solution for fixed and variable product sizes
- High availability with label supply roll carrying up to 450 running meters
- Suited for 3-shift operation
- Robust system
- Excellent service life
Technical data
Printing technology
Thermal transfer or thermal direct
Print resolution
8 dots/mm (203 dpi)
12 dots/mm (300 dpi)
24 dots/mm (600 dpi)
Printing speed
up to 400 mm per second
Dispensing head sizes
Tamp-Blow standard from 12.5 x 7 to 20 000 mm2; depending on label quality, label lengths should be reduced
Label gap
minimum 3 mm
Label roll
300 mm outer diameter with up to 450 running meters, roll core 76 mm (3”), outside winding
Optional: inside winding, larger roll core diameter and 350 mm label roll outside diameter
Data interfaces
all conventional interfaces
Control interfaces
floating outputs (relay), opto-coupler inputs, M12 connections for photo cells and alarm lamps
Service intervals
as per interval display
Dispensing output
Up to 80 labels per minute; dispensing output depends on label size, text change and dispensing stroke
Position accuracy of the dispensed labels
Standard: up to ± 0.8 mm with stationary product (depends on distance of application, applicator type and label size) optional: ± 0.5 mm
Printing dispenser activation
Reflex sensor, light barrier, inductive or capacitive sensor, micro-switch, floating contacts (PLC)
Alarm system
Standard: Error message in text display, floating contacts (PLC), Optional: 3-color alarm lamp
Compressed air consumption
0.3 to 3 l per dispensing cycle, depending on label size, type of applicator and setting
Compressed air connection
6 bar, compressed air must be clean, dry and oil-free (DIN ISO 8573-1)
Weight
from 35 kg (depending on type)
Electrical connection
90 to 263 VAC, 50/60 Hz, 5 Amp
Ambient conditions
Temperature: 10°C to 35°C, 15% to 95% relative humidity, non-condensing
Certification
CE mark
Options
- RFID labeling
- Bad Tag discarding
- Quick-change label format head springloaded dispensing head
- 3-color alarm lamp
- Dust and spray water protected enclosure (also with heating) for application in particularly tough environmental conditions
- IPC in the protective enclosure
- Legitronic® label printing software
Adobe Reader is required to open and view PDF files. This can be downloaded free from adobe.com.
Available Documents
Legi Air 4050s PrinterGeset 112 Bottom Labelling System
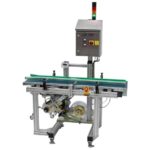
The Geset 112 labelling system is used to label square products on the bottom side automatically. Depending on the type and dimension of the product, different label sizes are used. The products are fed manually or by a conveying system provided by the customer at an infeed passage on the labelling system. Care should be taken on accurate alignment of the products. It is essential that the products are forwarded separately to the applicator with a gap between each other.
When the light barrier is reached, an application trigger is tripped. The label applicator applies then in Wipe On procedure a label onto the product. The label on bottom side is pushed on the product by the self-weight of the product. After labelling the products move on and can be removed from conveyor by the customer.
View ProductGeset 125 Horizontal Labelling System
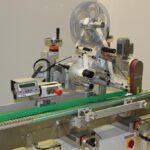
The Geset 125 labelling system is used to label cylindrical products automatically. Depending on the type and dimension of the product, different label sizes are used. The products are fed manually or by a conveying system provided by the customer at an infeed passage of the labelling system. Care should be taken on accurate alignment of the products between the two freely mounted rollers of the roll conveyor. The side guide’s position the products flush with the outside edge of the roll conveyor.
The roll conveyor feeds the products to the labeller. There the label is applied with the part running forward onto the product and it is pushed by rotation and the back pressure of the wrapping unit onto the product. The back pressure of the wrapping unit (the speed of the wrapping unit is twice as fast as the speed of the base conveyor) enables the product in rotation. The roll conveyor forwards the finished labelled products to the outfeed. Here the products are removed manually or by the customer’s conveying system.
View ProductGeset 111 Top Labelling System
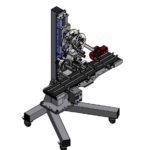
The Geset 111 labelling system is used to label square products on the top side automatically. Depending on the type and dimension of the product, different label sizes are used. The products are fed manually or by a conveying system provided by the customer at an infeed passage on the labelling system. Care should be taken on accurate alignment of the products. It is essential that the products are forwarded separately to the applicator with a gap between each other.
When the barrier is reached, an application trigger is tripped. The label applicator applies a label on the product in Wipe On procedure. The label on the top side is pushed on to the product by a brush or roller. After labelling, the products move on and can be removed from the conveyor by the customer.
View ProductGeset 117 Top and Bottom Labelling System
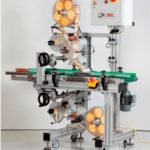
The Geset 117 labelling system is used to label square products on the top and bottom side automatically. Depending on the type and dimension of the product, different label sizes are used. The products are fed manually or by a conveying system provided by the customer at an infeed passage on the labelling system. Care should be taken on accurate alignment of the products. It is essential that the products are forwarded separately to the applicator with a gap between each other.
When the light barrier is reached, an application trigger is tripped. Both label applicators apply then in Wipe On procedure a label onto the product. The label on top side is pushed on the product by a brush or roller. The label on bottom side is pushed on the product by the self-weight of the product. After labelling the products move on and can be removed from conveyor by the customer.
View Product