X1Jet MX
The Markoprint X1JET MX is an inkjet printer that runs independently. It’s ideal for coding large printing images directly on carton material in the food, beverage, chemical, and construction industries. On flat or absorbent surfaces, the MX Class piezo inkjet technology codes rapidly, correctly, and reliably.
The X1JET MX comes in three different styles: Compact, Vario, and Top. The print head on the Compact variant is fixed vertically. The Vario version’s print head may be rotated 90 degrees to the left for coding on ascending conveyor belts. The Top version codes to the packaging or product from above. True Type fonts are used to print text, logos, barcodes, and data matrix codes in the system.
The Markoprint X1JET MX makes printing simple with its 3-logic intuitive operation and LED status light. Data can be transferred via USB stick. It also has a maintenance station that includes a power supply.
Markoprint X1JET MX
Compact and well-prized piezo inkjet coder for large printing images
-
-
- Independent print system with Trident Piezo technology
-
-
-
- Cleaning station integrated with print system
-
-
-
- All-in-one – print head, ink system, cleaning station, control electronics and power supply
-
-
-
- Simple and intuitive 3-button operation with LED control lamps for user-friendly system controls
-
-
-
- Available as 50 or 100 mm print head
-
-
-
- As Compact, Top or Vario version
-
-
-
- With Scantrue ink
-
Adobe Reader is required to open and view PDF files. This can be downloaded free from adobe.com.
Available Documents
X1JET MX leafletInk Guide 2015
Markoprint NonStop Printing
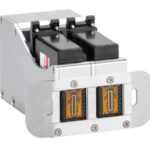
To enable continuous marking in ongoing production, our Markoprint NonStopPrinting printhead holds two alternately printing cartridges. Because the other ink cartridge is printing on the same position, each ink cartridge can be changed, cleaned, or serviced without pausing the machine.
An intelligent automatism prevents both cartridges from going empty at the same time. The first cartridge will always print two consecutive print jobs, taking turns with the second cartridge, which will only print one. This sophisticated automatism avoids both cartridges from running out at the same time. This will keep the ink from drying out in both cartridges. When the cartridge with the larger print volumes is empty, a warning will show, and the other cartridge will continue printing until it is replaced. The new cartridge will print the lower quantities to allow for you to replace the “older” cartridge. A sophisticated workflow that will boost your efficiency and productivity.
View ProductMarkoprint Integra Vivid
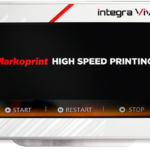
Unleash the Power of Modern Touch Operating Technology and an Innovative Swipe User Interface. Say Goodbye to Complicated Print Jobs and Say Hello to Effortless Operation of X1JET and PP Class Printing Systems. With the Freedom to Position the 7” High-Resolution HMI Color Display Anywhere You Choose, Prepare to Be Awed by the Ultimate Printing Flexibility and Innovation. Upgrade to integra Vivid Today and Embrace a New Era of Printing Excellence.
View ProductMarkoprint Integra PP 108
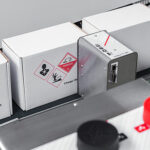
The Markoprint Integra PP108 is the first inkjet printer with SEIKO printing technology and a circulating ink system. It features a POZIFLOW circulating ink system which prevents the accumulation of air in the nozzles and ensures a permanent, clean print image without missing print due to blocked nozzles. The system’s ink tank can be installed above, below, or at the same height as the print head without any problems. The new SEIKO printhead has a print height of 108 mm and achieves a remarkable speed of up to 150 meters per minute with a high resolution of 360 dpi.
Suited to Dual Colour Printing Applications such as Hazard Labelling, Dual Colour overprinting and Direct Printing Applications to corrugate, and web printing applications, the PP108 is the latest high end, economical Inkjet System using the latest Drop on Demand Printing Technology.
View ProductZebra ZT510 Industrial Printer
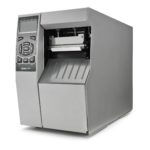
ZEBRA ZT510 – NEXT-GENERATION PRINTING THAT IS BUDGET-FRIENDLY
Designed to strike the ideal balance between performance and value, the Zebra ZT510 includes the core features you need in an industrial printer at a cost-effective price point.
View Product